Water Contamination Removal from Lubricant Sump Tank Without Production Downtime
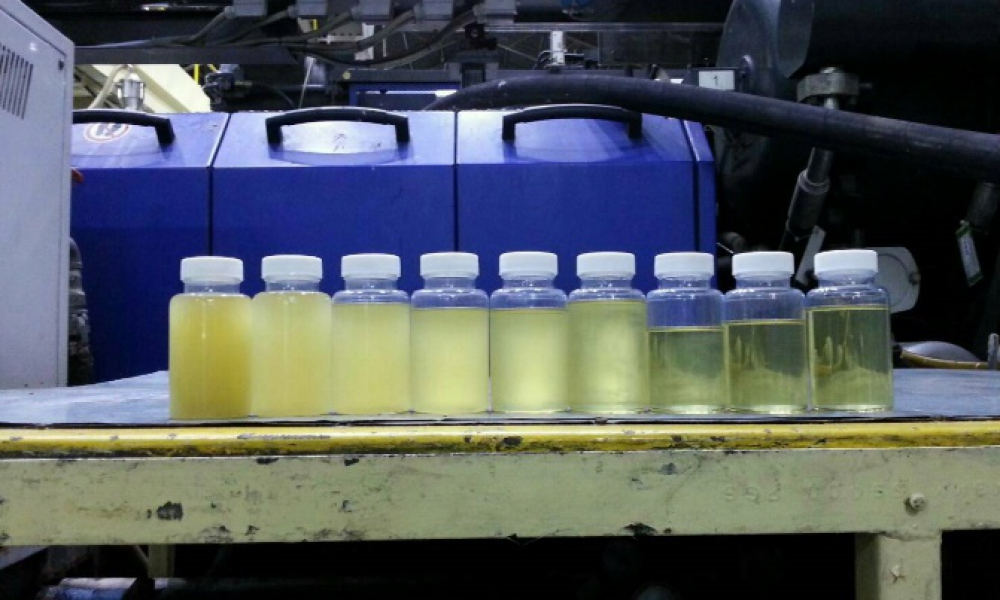
Customer Challenge
A manufacturing plant experienced water leakage from a heat exchanger, causing severe water contamination in the lubricant sump tank. After testing, the water concentration was found to be 55,000 ppm (5.5%), which posed serious risks:
🔹 Lubricant Degradation – High water content accelerated oxidation and reduced oil performance.
🔹 Increased Wear & Corrosion – Water in lubrication systems led to rust formation and reduced bearing lifespan.
🔹 Production Downtime Risks –
- The traditional cleaning method (oil changes and filter replacements) required 3 full oil changes, 12 filter replacements, and 9 days of downtime.
- Stopping production for 9 days would severely impact assembly line supply and business operations.
- The customer needed an alternative without shutting down production.
Lubefix Solution
To address the issue without stopping production, Lubefix implemented an advanced water removal purification system. The service was performed in-line, allowing the equipment to continue running while the purification process occurred.
Process & Implementation
1️⃣ Initial Water Level Check:
- Before treatment: 9,900 ppm (0.99%) (after initial customer efforts).
- Target water level: 1,000 ppm (customer’s required specification).
2️⃣ Purification Process:
- Installed high-efficiency water removal filtration technology.
- Continuous operation without stopping production.
3️⃣ Results Achieved in 4 Days:
- Final water level reduced to 460 ppm – Well below the customer's acceptable limit.
- Equipment remained operational – No production shutdown occurred.
Results & Impact
Parameter | Before Purification | After 4 Days of Purification |
---|---|---|
Water Concentration | 9,900 ppm (0.99%) | 460 ppm (below the 1,000 ppm requirement) |
Production Downtime | Required 9 days | 0 Days (No Downtime) |
Oil Changes & Filter Replacements | 3 oil changes, 12 filters | Not required |
✅ Avoided 9 days of production shutdown
✅ Saved on oil replacement and filter costs
✅ Prevented potential equipment failures and extended lubricant life
Customer Feedback
The customer was highly satisfied with Lubefix’s water removal solution, as it enabled them to continue operations without any downtime. The purification system efficiently removed excess water while maintaining lubricant integrity.
Conclusion
By using Lubefix’s advanced purification system, the customer successfully removed water contamination from their lubricant sump tank without stopping production. This case highlights the importance of in-line purification solutions for minimizing downtime and optimizing production efficiency.