Achieving NAS 1638 Class 7 Cleanliness During Oil Fill and Drain Process
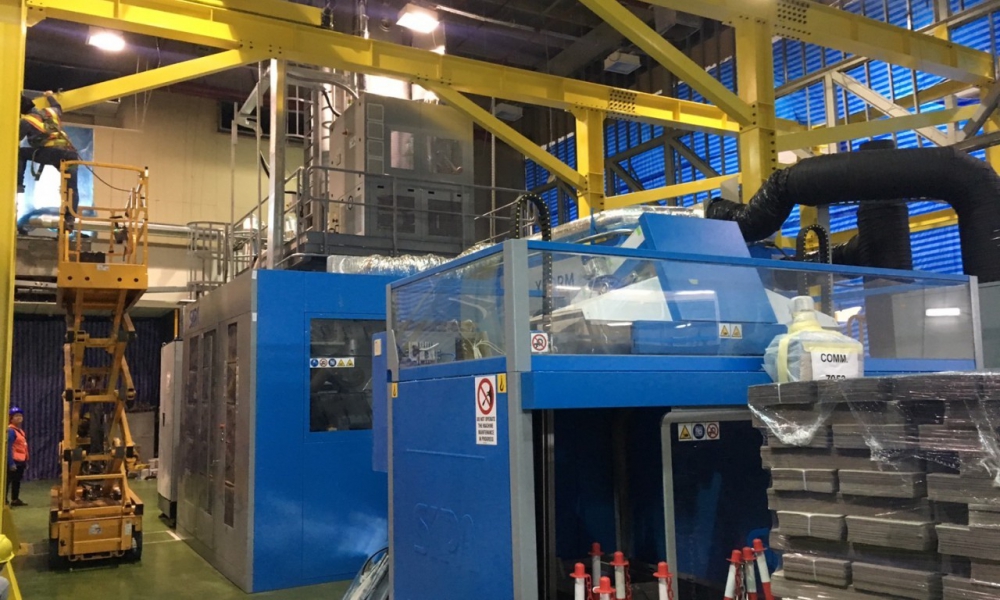
Customer Challenge
A customer required a complete oil fill and drain process, ensuring that the new lubricant met the NAS 1638 Class 7 cleanliness standard.
Challenges and Risks:
🔹 Residual Contaminants in the System – The presence of old oil and sludge could contaminate the new lubricant.
🔹 Uncontrolled Oil Filling Process – Introducing new lubricant without filtration could lead to dirt ingress.
🔹 Lubricant Cleanliness Standard Requirement – The customer’s machinery required NAS 1638 Class 7 oil cleanliness for optimal performance and equipment longevity.
Lubefix Solution
To achieve the target cleanliness level, Lubefix implemented a controlled oil drain, fill, and filtration process to meet NAS 1638 Class 7 standards.
Step-by-Step Implementation:
1️⃣ Draining Out Used Oil:
- Safely drained old lubricant from the machine, ensuring minimal contamination carryover.
- Used a controlled transfer system to prevent recontamination.
2️⃣ Initial Filling of New Lubricant:
- Introduced new lubricant using a closed-loop system to minimize exposure to contaminants.
- Pre-filtered the new oil through a 3-micron filtration system before filling.
3️⃣ Oil Filtration to NAS 1638 Class 7:
- Installed an offline oil filtration system to continuously circulate and filter the lubricant.
- Used high-efficiency filters to remove solid contaminants and micro-particles.
- Conducted periodic particle count testing to monitor oil cleanliness.
Results & Impact
Parameter | Before Lubefix Solution | After Lubefix Solution |
---|---|---|
Oil Contamination Level | Higher than NAS 1638 Class 7 | Controlled to NAS 1638 Class 7 |
Residual Particles | Present in the system | Removed through filtration |
Lubricant Cleanliness | Uncontrolled during oil fill | Pre-filtered and purified before use |
Machine Reliability | Risk of early wear and failures | Extended component lifespan and reliability |
✅ Successfully achieved NAS 1638 Class 7 cleanliness for the new lubricant
✅ Ensured a contamination-free oil change process
✅ Extended lubricant life and improved machine reliability
✅ Reduced wear, varnish formation, and maintenance costs
Customer Feedback
The customer was highly satisfied with Lubefix’s oil drain, fill, and filtration service, as it ensured that their machinery received clean and contamination-free oil, improving system reliability and efficiency.
Conclusion
By implementing Lubefix’s controlled oil filtration and filling process, the customer successfully transitioned to a clean and reliable lubricant system, ensuring compliance with NAS 1638 Class 7 cleanliness standards. This solution helped them prevent equipment failures, reduce downtime, and optimize lubricant performance.