Preventing Acid Formation and High Water Content in Fire-Resistant Fluid Using Air Dryer Technology
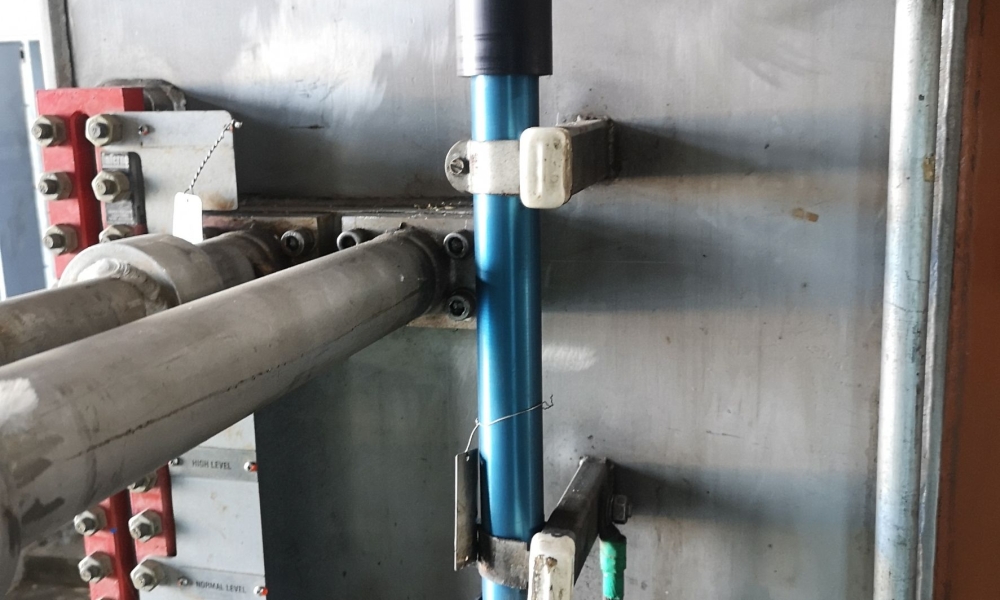
Customer Challenge
A manufacturing facility using Fire-Resistant Fluid encountered significant contamination issues after prolonged use. Oil lab results indicated:
🔹 Acid Formation – The lubricant exhibited increasing acidity, potentially leading to accelerated fluid degradation and component corrosion.
🔹 Excessive Water Content – The water level was above the acceptable limit, reducing the fire-resistant fluid’s efficiency and increasing the risk of varnish formation.
Risks & Potential Impacts
❌ Degraded Fluid Performance – High water and acid levels compromised the fluid’s fire-resistant properties.
❌ Increased Maintenance Costs – Frequent fluid changes and system flushing were required.
❌ Potential Equipment Damage – Acidic fluid could corrode system components, leading to premature failures.
Lubefix Solution
To mitigate water accumulation and acid formation, Lubefix recommended installing an air dryer system to control humidity in the headspace of the fluid reservoir.
Implementation Approach
1️⃣ Installed an Air Dryer System:
- Positioned the air dryer to remove moisture from the headspace above the fluid.
2️⃣ Applied the Mass Transfer Principle:
- When the headspace is dry, the water in the Fire-Resistant Fluid naturally evaporates and migrates into the headspace.
- The air dryer removes this moisture via the air breather, continuously reducing the fluid’s water content.
3️⃣ Continuous Moisture Management:
- By maintaining a dry headspace, water contamination is consistently drawn out from the fluid, preventing excessive water buildup.
- This method also slows down the formation of acids, prolonging fluid life and improving equipment reliability.
Results & Impact
Parameter | Before Air Dryer Installation | After Air Dryer Installation |
---|---|---|
Water Content | Above acceptable limit | Maintained within safe limits |
Acid Formation | Progressive increase | Slowed down significantly |
Fluid Life Expectancy | Frequent replacements needed | Extended service life |
Maintenance Costs | High due to frequent oil changes | Reduced costs and longer oil life |
✅ Effectively controlled water contamination using the Mass Transfer Principle
✅ Extended fluid life, reducing the need for frequent replacements
✅ Minimized acid formation, preventing corrosion and varnish buildup
✅ Lowered maintenance costs and improved equipment reliability
Customer Feedback
The customer was highly satisfied with the cost-effective and efficient solution, as the air dryer installation significantly improved the longevity and stability of their Fire-Resistant Fluid without requiring frequent fluid changes or additional complex treatments.
Conclusion
By implementing the Lubefix air dryer system, the customer successfully maintained optimal fluid conditions, preventing water contamination and acid formation in their Fire-Resistant Fluid system. This case study demonstrates how proactive humidity control can significantly improve lubricant reliability, reducing maintenance costs and enhancing system efficiency.