Achieving NAS Class 6 Cleanliness During Oil Change and Flushing
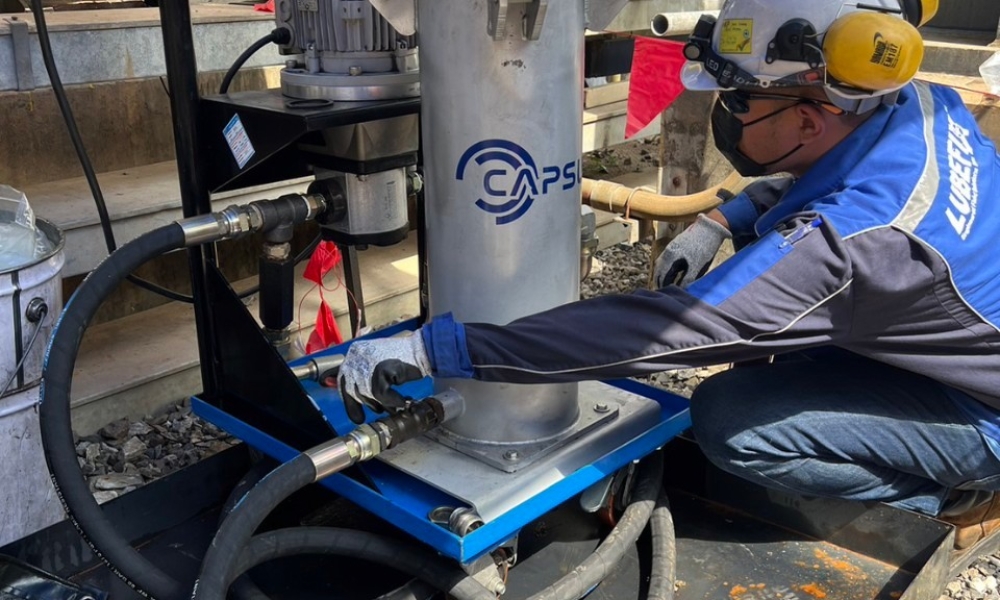
Customer Challenge
A customer required a complete oil change and flushing for their machinery. Their key objectives were:
🔹 Safe and Efficient Used Oil Removal – Draining the old lubricant without contamination risks.
🔹 New Oil Filling with Contamination Control – Ensuring that new lubricant was introduced in a controlled manner to prevent dirt ingress.
🔹 Lubricant System Flushing – Cleaning the internal system effectively before full operation.
🔹 NAS Class 6 Cleanliness Standard – The final oil cleanliness level needed to meet NAS 1638 Class 6 for optimal machine performance and reliability.
Challenges and Risks
❌ Residual Contaminants – Without proper flushing, residual particles from the old lubricant could contaminate the new oil.
❌ Particle and Varnish Formation – Any remaining dirt, sludge, or varnish in the system could reduce the efficiency of the new lubricant.
❌ Lubricant Performance Risks – Contaminated oil could lead to bearing wear, valve sticking, and potential failures.
Lubefix Solution
To meet the customer’s requirements, Lubefix implemented a comprehensive oil flushing and filtration process to achieve NAS Class 6 cleanliness.
Step-by-Step Execution
1️⃣ Draining Used Oil Efficiently:
- Collected used lubricant from the machine into an IBC tank, ensuring controlled disposal and preventing contamination.
2️⃣ New Oil Filling with 3-Micron Filtration:
- Filtered new lubricant through a 3-micron filtration system before introducing it into the customer's tank.
- This prevented large particles and contaminants from entering the system.
3️⃣ Lubricant System Flushing:
- Used the new oil to flush internal components, ensuring the removal of any residual dirt or varnish.
- This process helped displace old oil deposits and enhanced system cleanliness.
4️⃣ Oil Purification & NAS Class 6 Control:
- After flushing, the oil was recirculated and purified using a 3-micron filtration system.
- Continuous monitoring ensured that the oil cleanliness level reached NAS Class 6 before the machine was put back into full operation.
Results & Impact
Process Step | Before Lubefix Solution | After Lubefix Solution |
---|---|---|
Used Oil Removal | Risk of residual contamination | Fully drained and safely collected in IBC tanks |
New Oil Filling | Risk of introducing dirt | Pre-filtered with 3-micron filtration |
Lubrication System Flushing | Particles & varnish remained in the system | Effectively removed contaminants through flushing |
Oil Cleanliness Level (NAS) | Above NAS 6 (high contamination) | Controlled at NAS Class 6 |
✅ Achieved NAS Class 6 oil cleanliness for optimal machine performance
✅ Eliminated contamination risks with controlled oil draining and flushing
✅ Extended lubricant life and improved machine reliability
✅ Reduced potential downtime by preventing premature wear and varnish formation
Customer Feedback
The customer was extremely satisfied with Lubefix’s oil flushing and purification service, as it ensured their machinery received high-quality oil with controlled cleanliness. The solution helped them maintain operational efficiency and minimize long-term maintenance costs.
Conclusion
With Lubefix’s advanced oil flushing and NAS Class 6 filtration process, the customer successfully transitioned to clean and contamination-free lubricant, ensuring maximum equipment reliability and performance.